Description
Boart Longyear’s new DriftMaster™ series of rods and bits for tunneling, bolting and drifting applications provides productivity gains while reducing operating costs. Under the demanding loads of top hammer drilling, the unique thread profile delivers reduced stresses and increased wear resistance compared to a standard rope thread. Lower stresses and improved wear properties translate to longer product life, more equipment operating time, and lower overall costs.
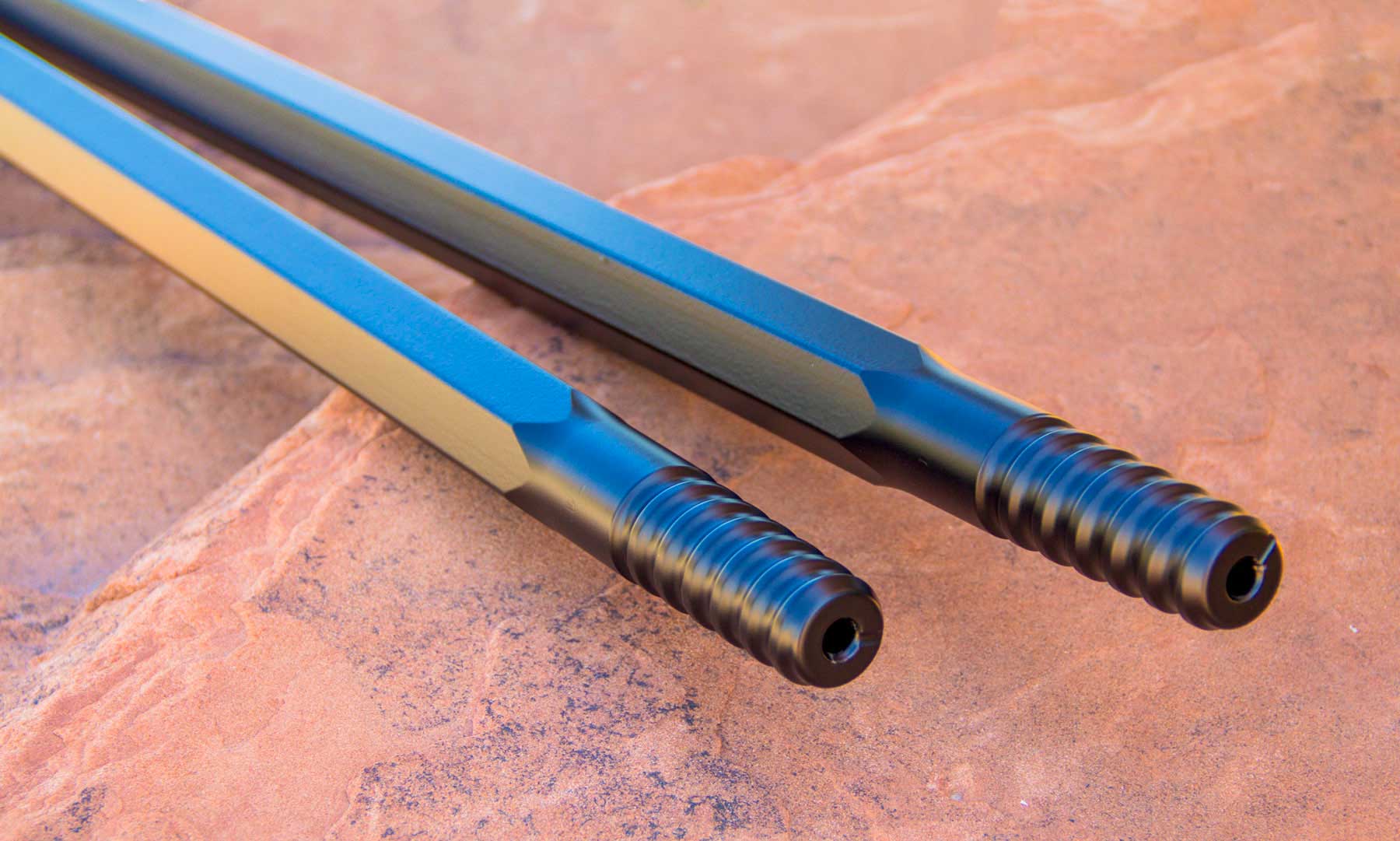
STRENGTH WHERE IT’S NEEDED
The Driftmaster offers increased strength through stress reduction in two key ways:
- The tapered profile provides an increased material cross-section at the base of the threads
- The asymmetric thread geometry acts to minimize stress concentrations
The lower tooling stress combined with deep case hardening allows for a significant increase in cyclic load handling capability. So, more load cycles mean more drilling time and more productivity.
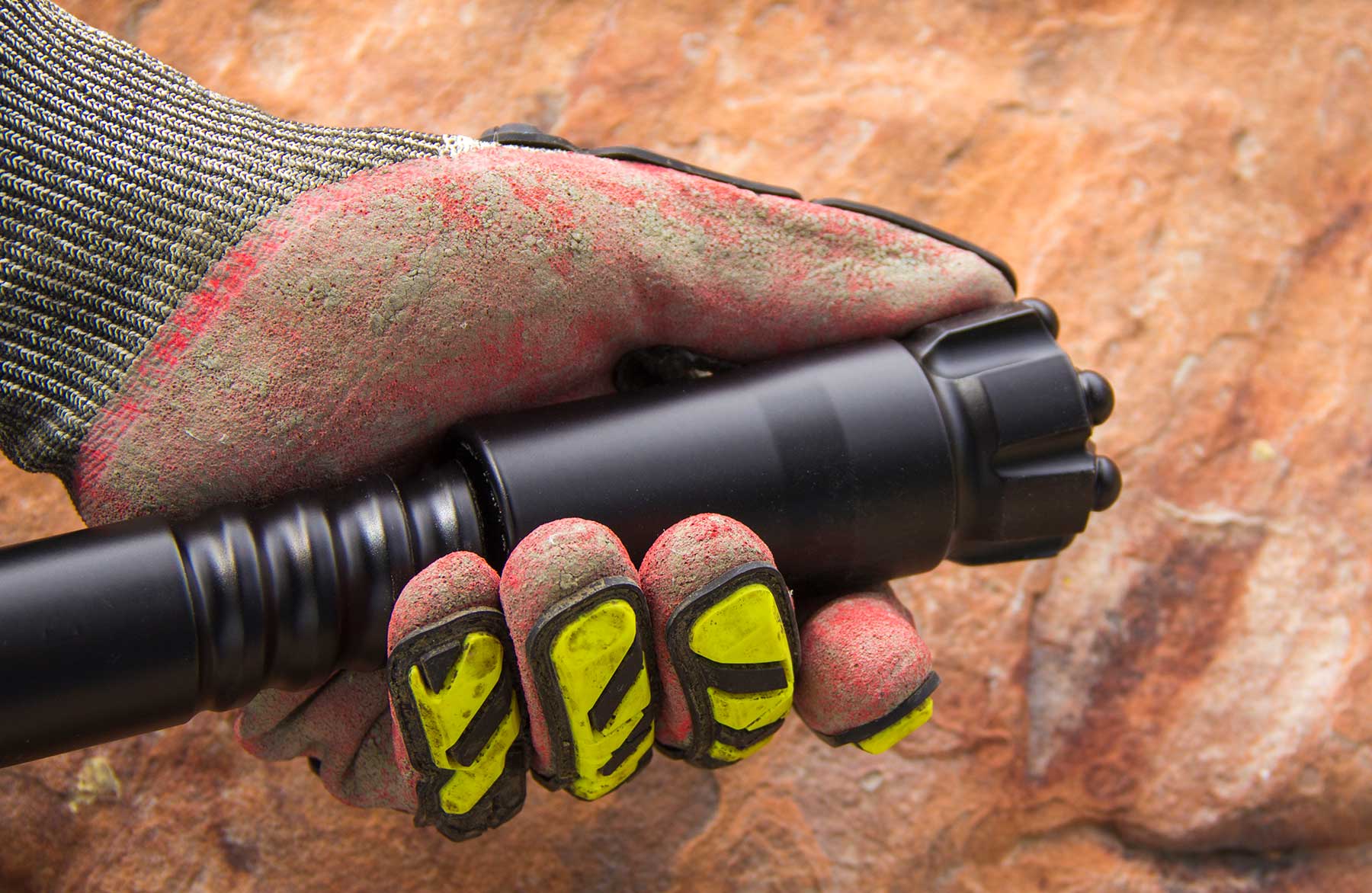
SUPERIOR RESISTANCE TO WEAR
Optimizing the load distribution and contact area through the tapered profile, the DriftMaster thread geometry is designed to maximize resistance to wear under the harshest drilling conditions.
Combined with the wear resistance associated with carburizing heat treatment, the DriftMaster thread geometry is proven to outlast.
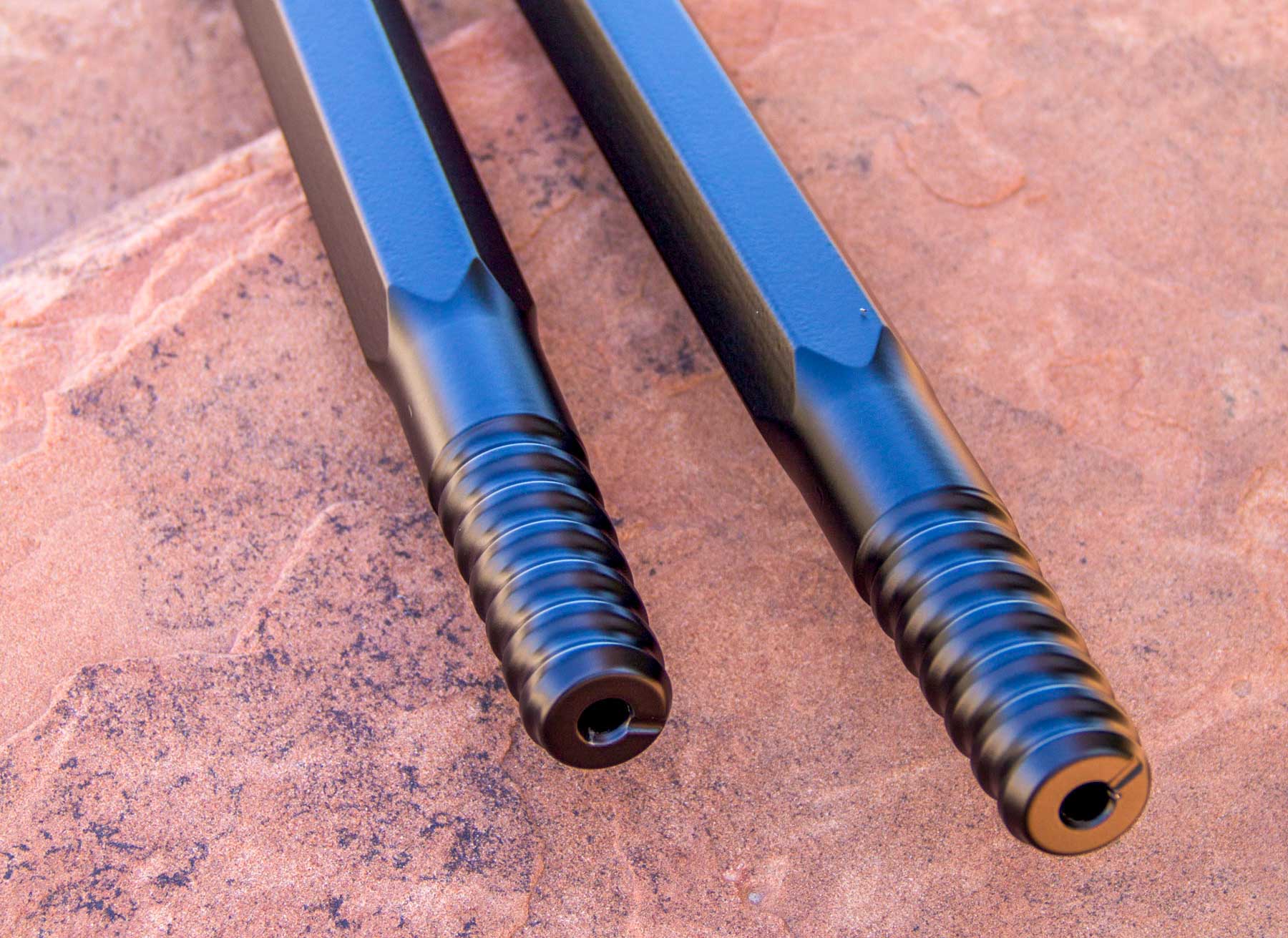
A MAKE-UP AND BREAKOUT ADVANTAGE
To further improve productivity, the tapered thread profile offers superior rod-bit make-up and breakout characteristics. This key thread feature results in more drilling time.
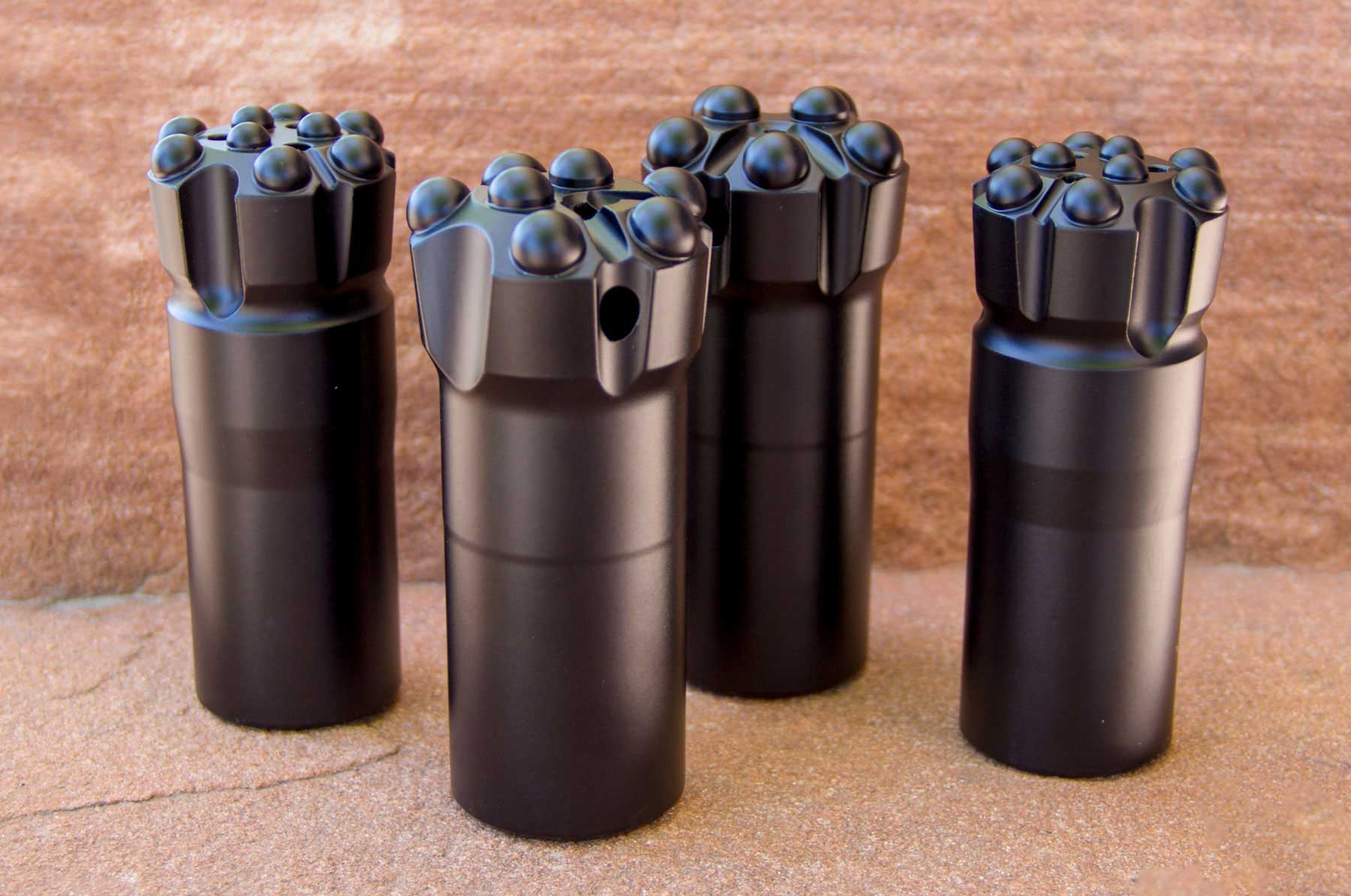
DriftMaster is being introduced in 35 mm hex cross-sections for use with standard, Retrac, and Straightrac button bits from 43 mm – 64 mm. The initial offering includes dome and pilot reamers – including optional RazorBack™, a patented high-productivity back-reaming bit.
Contact your Boart Longyear representative for additional options.